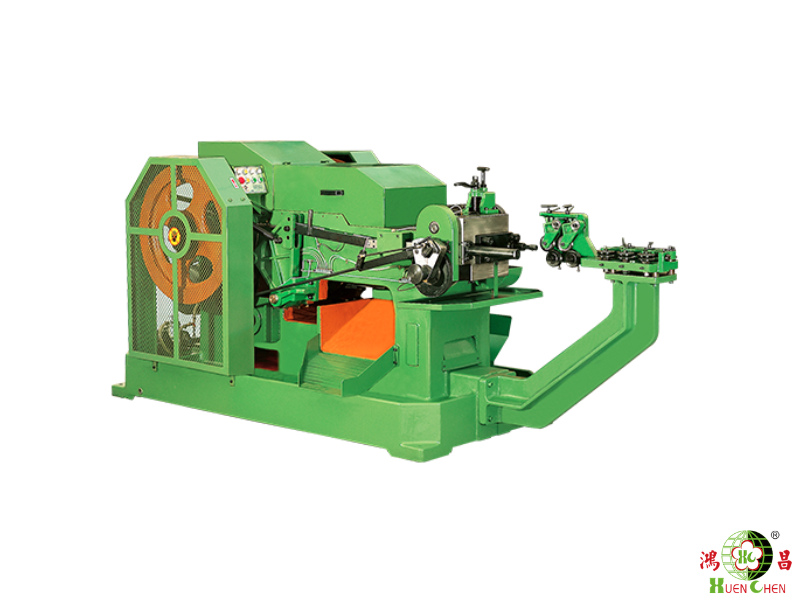
What Is a Heading Machine and How It Works?
A heading machine is a powerful tool used for metalworking applications. It is used to shape and cut metal into specific shapes and sizes. This type of machine is used in a variety of industries, including automotive, aerospace, and manufacturing, and it has become an invaluable tool for both large and small businesses.
In this article, we will discuss what a heading machine is, how it works, and the different types available. We will also look at some of the advantages and disadvantages of using a heading machine so you can decide if it is right for your needs.
Note: This article will focus more on cold-heading machines because cold working is the most common type of metalworking.
What Is a Heading Machine?
Heading machines are used to create screws, rivets, bolts, special fasteners, and intricate parts from wire coils. 2-die, 4-blow machines are ideal for components with large heads that require three blows, such as Allen screws.
One advantage of these machines is that the third blow can be used as an introductory punch for parts with large heads and a short shank. This process is incredibly efficient and allows for complex components to be produced quickly and easily.
In addition to their ability to produce complex components, these heading machines are also capable of producing parts with a higher degree of accuracy than other methods.
While the initial cost of purchasing a heading machine may be higher than other methods, the cost is typically offset by the improved accuracy and efficiency of the production process. This accuracy can be especially beneficial when creating parts with tight tolerances and complex shapes. Heading machines can also produce parts with a higher degree of repeatability, allowing for parts to be easily replaced and interchanged.
Heading Machine Working
Producing parts with precise and consistent tolerances at a rate of 400 pieces per minute is made possible by the cold heading process. This procedure uses cutting-edge automated "cold headers" or "part formers." To begin, a wire is inserted into the die, followed by hammering to shape it into various forms as desired. The technology behind this progressive tooling allows for efficient manufacturing in high volumes that would otherwise be impossible.
Cold heading is an essential process in manufacturing and fabrication, often used to form intricate shapes from a given volume of material. The process is highly versatile and can be used in combination with other cold-forming operations, such as sizing, piercing, trimming, thread rolling, blank rolling and pointing.
Cold Heading Terms
If heading machine terminology is confusing, don't worry. Here are some helpful definitions of the various terms related to heading machines:
- Cut-off: The process of cutting a specific length of wire from a coil of wire before it is fed into the heading die.
- Extrusion: This process involves forcing material into a die, causing its diameter to decrease.
- Heading Die: A stationary tool that has the precise geometry for a specific part that is machined into its cavity. This die is used to form and shape parts through the heading process.
- Diameter of Upset: This refers to the amount of material that is used to form the head of a fastener. The larger the diameter of the upset, the larger the head of the fastener can be made. For example, a "4 ½ diameter of upset" involves a lot of material being moved to form the head, while "1 diameter of upset" only moves a small amount of material.
- Punch: A movable tool that strikes the cut-off slug, thus upsetting the material and forcing it into the heading die to form a part.
- Knockout Pin: This tool serves two purposes in the heading process. Firstly, it acts as a support for the blank while it is being formed into a part. Secondly, it is used to eject the finished part out of the die.
- Upsetting: This is the process of striking an object on its end, causing its diameter to increase in size. This process is used in cold heading to form fastener heads.
- Grain Flow: The grain flow of the material being worked on can be either interrupted or uninterrupted. Interrupted grain flow occurs in machining, while uninterrupted grain flow occurs in the cold heading. Cold-formed parts are stronger because their internal grain structure follows the contour of the part, making them stronger compared to parts with an interrupted grain flow.
Advantages of Using a Cold Heading Machine
Since its invention in the late 19th century, cold heading has become an integral part of many manufacturing processes today. It offers a number of advantages over other machining processes, such as:
- Reduced Raw Material Waste: Cold heading machines result in reduced raw material waste, making it an environmentally friendly option.
- High-Speed Production Rates: Cold-heading machines have high-speed production rates, allowing for quick and efficient parts production.
- Improved Physical Properties: The process of cold heading results in improved physical properties of the parts, making them stronger and more durable.
- Reduction in Cost Vs Machining: Cold heading is often more cost-effective compared to machining, making it a preferred option for manufacturers.
- Capabilities Include a Large Range of Diameters: Cold-heading machines can produce parts with a large range of diameters, making them versatile in their applications.
- Tight Tolerances:The use of a cold heading machine results in tight tolerances, making it possible to produce precise and accurate parts.
- Customizable to Customer's Specifications: These machines can be made to the customer's specifications, both for standard and non-standard configurations.
- Large Volume Capabilities: These machines have the capability to produce large volumes of parts, making it suitable for mass production.
- Secondary Operations Available: Many secondary operations are available to complete fully customized parts, making cold heading a complete solution for manufacturers.
Basic Forming Techniques of Heading Machine
Cold-heading manufacturing is an efficient way to form materials by pushing it into a die. Extrusions and upsets are two main methods in this process, utilizing precisely calibrated dies that guide the material as it's being molded. As you apply pressure, the raw material fills any voids within the space of your designed die until its shape matches your desired outcome.
Upsets
Upsets are a common technique used in cold heading to form parts. By reducing the slug's height and increasing its diameter, any given part can have a head created for it. Depending on their shape and location, open tooling, between tooling, or enclosed tools may be utilized as needed. Additionally, when integral components require multiple heads along with varying diameters, different types of upset configurations must then be included during fabrication progression accordingly.
Extrusions
If you're looking to improve your cold heading technique, consider an extrusion! This method can be used in two directions: forward and backwards.
Forward Extrusions
To manufacture a forward extrusion, the starting material is inserted partly or completely into a die. This process then reduces its diameter and elongates it as it's forced through an outlet of a smaller size.
The result?
A more precise product with greater length!
Backward Extrusions
Create holes or cavities within a part with backward extrusions that push materials around an inserted punch or pin, all while being constrained within the molding die. Backward extrusion is not only efficient but also highly effective.
Conclusion
A heading machine is a tool used to shape and cut metal into specific shapes and sizes for various industries, such as automotive and aerospace. Cold heading is the most common type of metalworking and uses automated machines to produce parts with precise and consistent tolerances quickly and efficiently. The process involves inserting a wire into a die, followed by hammering to shape it.
Cold heading offers advantages such as reduced raw material waste, high-speed production, improved physical properties of parts, cost-effectiveness compared to machining, and versatility in producing parts with a large range of diameters.